DuPont sees production benefits from new turnaround process
Initiating company-specific best practices and streamlining its turnaround processes over the last few years has allowed DuPont’s Manufacturing Center in Mobile, Alabama to dramatically improve its turnaround scope management system and start up all its production lines on time, said Chris Vaughn, maintenance team leader and turnaround leader at DuPont.
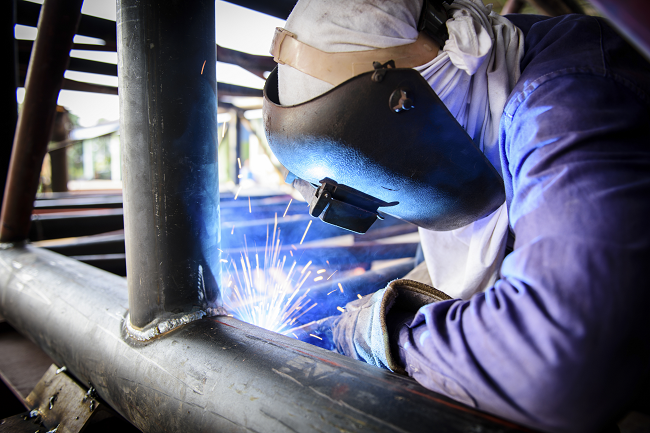
Related Articles
Speaking at Petrochemical Update’s Gulf Coast Shutdowns and Turnarounds Conference in New Orleans on June 8, Vaughn discussed DuPont’s two-year effort from 2013 to 2015 to improve its turnaround execution at its Mobile manufacturing facility, which makes a variety of insecticides, fungicides and specialty chemicals.
The new turnaround processes Vaughn and his team introduced raised the site’s turnaround readiness assessment from 52% in 2012 and 83% in 2014 to 94% in 2015, Vaughn said. It also dramatically improved its scope management record, reducing add-on work – or the work added after the freeze date – from 77% in 2013 to only 5% in 2015.
The new turnaround process allowed Vaughn to release $17 million in capacity and finish the majority of turnarounds safely, on time or ahead of schedule, and gain buy-in from the whole project delivery supply chain, Vaughn said.
The new process also managed to integrate all of the work groups – maintenance, manufacturing, capital and contractors – into one schedule, he added.
Turnaround performance
With the next 3-5 years expected to see a high number of shutdowns, turnarounds and outages at petrochemical plants and refineries in the U.S., it is crucial for producers to build effective plans and processes to deliver maintenance projects on time, on budget and safely.
Even though companies often plan maintenance projects months or even years in advance, some 68% of U.S. refiners and chemical plants still fail to deliver their planned shutdowns, turnarounds and outages on time, according to Oracle Corporation.
At the same time, capital project work as a percent of turnaround work has grown from just 2% in 2006 to nearly 25% in 2014, making turnarounds more complex, according to turnaround and project management consultancy Asset Performance Networks (AP-Networks).
Schedule predictability on mega turnarounds ranges between 0% and 50% and cost predictability between 0% and 40%, Craig Small, senior consultant at AP-Networks, said during the conference.
AP-Networks’ study of medium and high-complexity turnarounds executed since mid-2012 shows that turnarounds most often fail to meet their cost, schedule and safety goals due to increased event complexity, inefficient organizational capability, lack of engaged leadership, ineffective scope development and scope freeze, as well as inadequate capital project integration.
Developing a turnaround mindset
In 2013, Vaughn and his team began a turnaround at DuPont’s Mobile site to release additional capacity to meet quickly rising market demand, and to optimize the company’s turnaround work processes.
The turnaround readiness assessment conducted by DuPont’s global turnaround leader two and a half months before the start of the turnaround showed that its current work process lacked structure, job planning progress, focus on operations, as well as key performing indicators.
According to the review, the team’s schedule did not include sufficient operations work list tasks to effectively schedule and track daily tasks, while the operations and maintenance teams did not work and coordinate with each other.
The initial effort to allocate responsibilities, set up a steering team to drive the strategy and a core team to execute it, and roll out best practices for work management such as regular schedule reviews and maintenance standards faced a lot of pushback internally.
The first step was to change the company culture, overcome resistance to change, develop a turnaround mindset and get leadership support, Vaughn said. This meant communicating the turnaround objectives broadly and well in advance of the maintenance work, implementing transparent and simple processes, introducing peer-to-peer accountability, using review processes in a “continuous feedback loop” and engaging all levels of employees in the turnaround.
“These are really the catalysts that help accelerate improvement, as well as sustain the better level we are at,” Vaughn said.
The basics: early work identification and schedule control
To develop a robust schedule and go beyond basic best practices, in 2014, Vaughn’s team began to assign clear roles and responsibilities for the turnaround steering and core teams, and to put more effort into defining and managing the work scope.
Vaughn also replaced the traditional day-to-day planners in the core team with dedicated planners and schedulers.
With work stretching across six production units and two major units, he initiated weekly core team meetings to identify areas for improvement, focus on the priority tasks and align the different team members.
Vaughn also introduced monthly steering team and daily rack-up meetings during the turnaround execution phase to keep the different project interfaces focused on the same goals.
Identifying and freezing the scope of the work early was also key to the proper planning and scheduling of the work activities, Vaughn said. This allowed the team to identify and set aside sufficient time to procure materials and other resources. As a new best practice, the team would set the freeze dates for the scope months ahead of the maintenance work.
Freezing the scope in the early stages of the project also helped minimize expediting costs, create visibility and gain buy-in from other teams, identify the work associated with PHA action items to ensure timely planning for the execution work, optimize the turnaround integrated schedule and plan enough time to coordinate the turnaround activities.
To ensure integration and trust among the different project interfaces, Vaughn also introduced a new add-on work request process that required that requests be approved by different levels and departments – from the plant manager and the site maintenance and engineering manager, to the unit operations leader – provided that they have RTO, and meet safety and environmental standards.
A turnaround coordinator would also keep track of all add-on work requests, whether approved or deferred.
One of the biggest challenges for the team was to build a reliable schedule, Vaughn said. A year after the start of the project, the turnaround was 15 days behind schedule, many of the project interfaces still lacked sufficient coordination and there was little trust in the turnaround schedule.
To define and manage the scope better, Vaughn’s team began implementing a work order identification strategy every quarter, implemented a Single Minute Exchange of Die (SMED) lean methodology to streamline the sequencing and logic of the integrated schedule, and focused on gaining accountability with the leadership on add-on requests to encourage early work identification.
Post-turnaround evaluation
Conducting post-turnaround evaluation to develop strategies to eliminate weak areas was another critical step to changing how DuPont executed its turnarounds, Vaughn said. Implementing a good review system at DuPont has allowed the company to plan its annual turnarounds in 8-10 months rather than a year (the industry average).
A couple of years ago, Vaughn began sending out pre-work surveys to all project disciplines to identify the key strengths and target initial improvement areas. He also launched an interactive critique process to get feedback on the identified improvement areas and began gathering all working groups in more structured meetings to discuss more granular issues specific to their tasks.
The feedback from the first turnaround allowed the team to glean more details to improve its processes and to develop take-out plans and a project study scoping report (PSSR) strategy.
As a next step, in 2015 DuPont started breaking its turnaround work process down into smaller pieces, reviewing and improving more granular issues such as how to develop an integrated schedule and an optimal contracting strategy for repairs; conduct a more MIQA risk assessments based on a review of past history to issue recommendations on potential discovery work and the severity of the damage; plan for contingencies that migh t require procuring more resources in advance; communicate current and future KPIs; engage employees and contractors; and perform corporate readiness assessments, among others.
Read highlights from the major projects track and the plant-based and small projects track at the Petrochemical Engineering & Construction 2016 conference, co-located with the Gulf Coast Shutdowns & Turnarounds Conference.